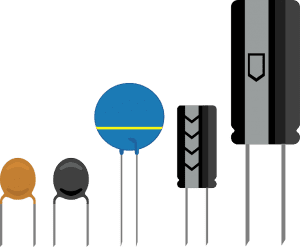
First: ceramic capacitors
Ceramic capacitors are made by extruding a high-dielectric constant capacitor ceramic (barium titanate titanium monoxide) into a tube, wafer or disc as the medium, and plating silver on the ceramic as an electrode by sintering method. It is divided into high-frequency porcelain and low-frequency porcelain.
High-frequency ceramic capacitors are suitable for high-frequency circuits in radio and electronic equipment. Capacitors with a small positive capacitance temperature coefficient are used in high-stability oscillating circuits as loop capacitors and pad capacitors.
Low-frequency ceramic capacitors are limited to bypass or DC blocking in circuits with lower operating frequencies, or occasions where stability and loss are not high (including high frequencies).
Such capacitors are not suitable for use in pulse circuits because they are easily broken down by pulse voltage. Common ceramic capacitors are:
For a through-core or pillar-type ceramic capacitor, one of its electrodes is a mounting screw. The lead inductance is extremely small, which is especially suitable for high frequency bypass.
Monolithic capacitors are multilayer ceramic capacitors. Its structure is to cover several pieces of ceramic film blanks with electrode paddle materials, which are wound into an indivisible whole after being laminated, and then encapsulated with resin. It is a A new type of capacitor with small size, large capacity, high reliability and high temperature resistance. The low-frequency monolithic capacitor with high dielectric constant also has stable performance and is small in size.
Second: Mica capacitor
In terms of structure, mica capacitors can be divided into foil type and silver type. The silver electrode is formed by directly plating a silver layer on the mica sheet by vacuum evaporation or burning infiltration. Because the air gap is eliminated, the temperature coefficient is greatly reduced, and the capacitance stability is higher than that of the foil type.
Mica capacitors are widely used in high-frequency electrical appliances and can be used as standard capacitors.
The dielectric of the glass glaze capacitor is sprayed into a thin film by a special mixture with a concentration suitable for spraying. The dielectric is then sintered with a silver layer electrode to form a “monolithic” structure.
The performance of glass glaze capacitors is comparable to that of mica capacitors, and can withstand various climatic environments. Generally, they can work at 200°C or higher. The rated working voltage can reach 500 V, and the loss tanδ = 0.0005 ~ 0.008.
Third: Paper capacitors
Paper capacitors are widely used in radio and electronic equipment. Generally, two aluminum foils are used as electrodes, and capacitor paper with a thickness of 0.008 ~ 0.012 mm is separated and wound in the middle.
The manufacturing process is simple, the price is cheap, and a larger capacitance can be obtained, generally below 0.25 μF, but the capacitance error is large and difficult to control. The better quality is ±10%, the loss is large (tanδ ≤ 0.015), and the temperature frequency The characteristic stability is poor.
The paper capacitors commonly used in the past are of non-sealed type, only impregnated and sealed with ceresin wax, paraffin wax and diphenyl chloride, etc., which are prone to aging, have poor stability, and are easily affected by humidity. After being exposed to moisture, the insulation resistance decreases, and atmospheric pressure also affects it. .
Paper capacitors with capacitor cores placed in metal or ceramic tubes to be sealed are of good quality and have minimal impact on external weather conditions. They can be used normally in occasions with a relative humidity of 95% to 98%.
Fourth: film capacitors
The structure of film capacitors is similar to that of paper capacitors, but low-loss plastic materials such as polyester and polystyrene are used as the medium. Polystyrene capacitors have excellent performance and can be used as excellent coupling capacitors in low-frequency circuits.
It is also particularly suitable for RC time constant circuits because of its minimal dielectric absorption and fast discharge. High temperature resistant film capacitors include polyester capacitors, polytetrafluoroethylene capacitors and polycarbonate (PC) capacitors.
Polyester capacitors are also called polyester capacitors. Their electrical performance is better than metallized paper capacitors. They are mainly used as bypass and DC blocking in circuits to replace paper capacitors.
The electrical performance of polycarbonate capacitors is better than that of polyester capacitors, and it can work at +120 ~ 130°C for a long time.
The electrical properties of polypropylene capacitors (CBB) are similar to those of polystyrene capacitors, but the capacitance per unit volume is larger, can withstand high temperatures above +100°C, and the temperature stability is slightly worse.
Fifth: Electrolytic capacitor
Electrolytic capacitors are capacitors that use a thin oxide film as a dielectric. Because the oxide film has unidirectional conductivity, the electrolytic capacitor has polarity.
Sixth: Aluminum electrolytic capacitors
It is formed by winding absorbent paper impregnated with paste electrolyte between two aluminum foils.
Ordinary aluminum electrolytic capacitors are not suitable for high-frequency and low-temperature applications, and should not be used at frequencies above 25kHz. They are usually used for low-frequency bypass, coupling and power supply filtering.